Dick,
I want to pick your brain as you are one of the few people I know who understand the question.
Danny Gough (Housedoc) HVAC Done right!
Hi Danny. It’s great to hear from a good friend and very valued long-time customer.
(Bold Italic type are my opinions, Regular type is by Danny.)
I am seeing an epidemic of mold inside air handler cabinets, in supply plenums and in the first 10 to 12 feet or so of supply air trunk.
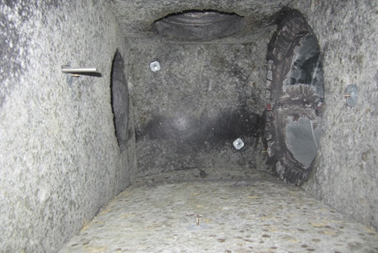
MOLD CAN BE DEADLY!!
One VERY bad one is: stachybotrys chartarum
Yes, we are hearing of mold becoming an increasing problem in residential HVAC systems. The HVAC industry’s archaic infatuation with switches and high-single speed, two-speed, and timed ramp blower motors has a lot to do with mold growth in the ductwork. Our self-compensating, modulating Whisperer 4-Z blower speed controls eliminate bypass problems by eliminating the bypass and controlling duct pressure to whatever you want, and precisely holding it there. Pesky bypass attempts to control duct pressure by short cycling excess air from the supply plenum to the return is a failure. A FanHandler Whisperer 4-Z control controls the duct pressure by monitoring duct pressure dozens of times per second, adjusting the blower’s speed to hold whatever pressure setting you make. Once set, the pressure will hold within 0.02” w.c..
The fact that mold is being spread 10 to 12 feet down the ductwork proves that too much air blasting though the evaporator coil. Also, that this mold has been around long enough to cause considerable damage to the HVAC system. Hopefully it is caught before causing significant health problems. If I were on that job, I’d inform the homeowner and any governing health authorities that I have discovered an almost certain health hazard.
Whoever is responsible for this mess had better immediately contract a mold remediating company. If folks get sick from the mold, the responsible party better have super deep pockets or a lot of mold and other insurance. What is not clear to me is: IF/when you discover mold and do not inform the homeowner, and/or health authorities; might you, in some way, share responsibility for subsequent damages. That could be devastating!
There are three common denominators that accompany an almost 100% occurrence.
- The air handler cabinet and supply duct are insulated internally with fiberglass duct liner. I do not see visible mold in bare sheet metal ducts. But air handler cabinets that are lined with fiberglass are covered with mold.
Interesting that you don’t see mold on the sheet metal. Give it a little more time!
- In addition to duct liner, the second factor that seems to guarantee mold inside the cabinet and supply duct is ZONING. In particular, zoning that includes a bypass damper, either barometric or electronic.
Bypass dampers are the Achilles heel of zoned systems. There are many HVAC contractors who WILL NOT install zoned systems because of associated bypass problems. The FanHandler “Whisperer” 4-Z variable speed control allows you to eliminate the bypass and its problems by precisely controlling the duct pressure. This is done by precisely regulating the blower’s speed.
- Every instance I have seen thus far is on single speed compressor systems. The blower motor doesn’t seem to matter. I have seen mold develop with both fully variable speed and X13 fixed torque motors.
One reason why you don’t see mold on systems equipment with a modulating compressor is: a high speed fan coupled with a variable speed compressor results in a warmer coil and very poor humidity control. A warmer coil results in less humidity removal. Less humidity removal makes for a pretty dry coil which leads to uncomfortable, hot, muggy, and smelly environment. The only way I know that solves this problem is to install one of our blower modulating controls.
Fully variable speed and the fixed torque motors are often controlled by a time/speed formula. When the speed increases with time, it delays by a couple minutes, when the blower will strip water from the coil. Nothing tells the motor to stop speeding up until it is way too fast for the conditions.
Your mention of a single speed compressor hits home. A long time ago (at least 15 years) we worked with zoning and compressor manufacturers who asked us to control the speed of an AC compressor. The ECM technology was not developed far enough at the time. We could control the speed of compressors but the electronic parts would have to be as big a boxcar. I’m sure that our Whisperer 4-Z can control any of the new variable speed compressors. Ryan can’t wait to make it happen. He will probably develop a system where one Whisperer 4-Z will control both compressor and the fan and probably put the cat out at night.
One of our contractor customers has installed his 12th Whisperer 4Z on First Company’s variable speed compressor heat pumps. It works like a charm!!! LONG LIVE First Company! They manufacture great equipment!
The bypass damper is simply a cheap way to handle excess air when a small zone is calling that cannot handle full airflow. All this does is relieve excess air by recycling it from the supply
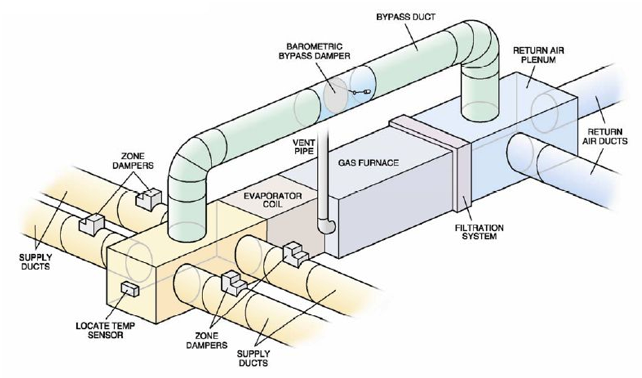
plenum right back into the return. The more the system runs with the bypass open, the colder the return air temperature gets. I muse that the colder the return air temperature gets, the colder the evaporator coil. The colder the evaporator coil, the more moisture forms on the coil.
That is a great explanation of what’s happening within the equipment! Might I add to the end of that paragraph: Therefore, that increased water is also blown off the coil and down the ductwork.
Now add the fact that once any bypass damper cracks open, you introduce another problem that further increases air velocity through the coil. The blower in the furnace section is creating a high pressure between the blower and the coil. Added to that, the bypass is contributing suction on the outlet side of the coil. High pressure on the inlet side of the coil and low pressure on the leaving side of the coil greatly increases velocity through the coil. Thus, more water, more mold, more mold spores and more potential health problems. Once mold matures and sheds spores, these spores are blown out of the HVAC system into the home. Then into the most sensitive and efficient filters ever produced. HUMAN LUNGS!
In most cases, there is a temperature sensor in the supply plenum that shuts off the compressor when the discharge air temperature drops to 40 degrees or so. Although the compressor shuts off, the indoor blower continues to run until the evaporator coil warms up above 40 degrees.
In some cases, the discharge air sensor is omitted. In those situations, the compressor is allowed to continue running, likely freezing the coil in extreme situations.
I am trying to uncover the correlation and possibly the cause of the mold as it relates to this bypass situation. That is where I am hoping you can enlighten me.
You’ve given us plenty of valuable information. I’ll try to expand on it.
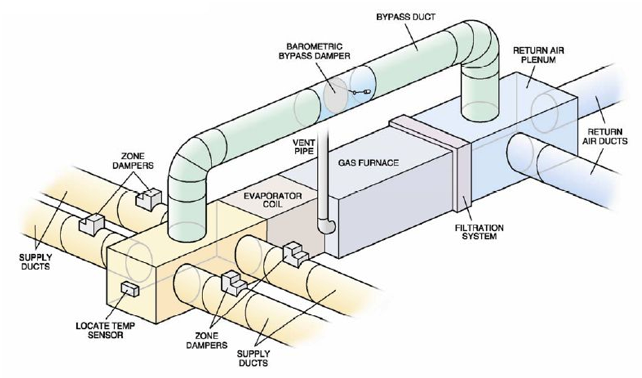
Taking another look at your equipment drawing it is easy to recognize that when any of the four zone dampers begins positioning towards closed the air pressure past the evaporator coil increases. This pressure opens the barometric bypass damper. Once a barometric bypass cracks open, we may as well accept that it is virtually all the way open. The air is now screaming through the bypass duct. It is way exceeding the 500 feet per minute water stripping threshold of the evaporator coil. Results? = A lot of water in the ductwork which = MOLD!
FanHandler Inc. is the industry leader in way advanced electronic motor speed controls especially designed for HVAC comfort and efficiency. During periods when there is no call for heating or cooling, the blowers speed can be set to the point where you can’t hear air movement or feel it a foot from any register.
The HVAC system can be any type (forced air furnace, heat pump, fan/coil unit.) New or 15 years old. Any equipment in reasonable condition
Can be modernized to provide unmatched comfort and efficiency.
For best results you might want to set the minimum speed at about say ¼ speed. At ¼ speed, per the fan laws, (not the fan maybe’s or wanta be’s. IT IS A SCIENTIFIC PHYSICS LAW!) fans will run for 64 hours for the same energy cost as at full speed for one hour. You won’t feel it nor hear it while saving energy and leveling the temperature throughout the home.
When air circulates through a home quietly, smoothly, imperceptibly and efficiently, It gently pulls air from the sunny side of the home brings it back to the HVAC equipment where it is mixed with air from the cooler areas. All rooms stay fresh and one temperature. The entire HVAC system, including all Indoor Air Quality equipment operate at peak efficiency.
The stakes are much higher in NC because, trying to solve a comfort problem, the licensing board for HVAC contractors requires zoning on all two-story houses.
As usual, FanHandler Inc. comes to the rescue with the Whisperer 4Z which can easily solve the problem. (VIDEO)
IN “MODULATION FOR AIR CONDITIONING HUMIDITY CONTROL”, you state in item #5
"Water adheres to the A/C coil better as the coil gets colder.”
Thanks Danny for referencing my white paper on
TEMPERATURE CONTROLLED BLOWER MODULATION FOR AIR CONDITIONING HUMIDITY CONTROL
Everything in there is dead-on true. The part that you mention concerning the colder the coil the greater the adhesion between the coil and water. That is true, but not an enormous difference. The 500 ft. per minute face velocity remains the threshold air velocity, above which water will be stripped off the coil and down the duct where it connects with a very good environment for mold growth. I don’t know of an exception. Skipping ahead a bit: The fact that you are seeing mold 12 feet down the ductwork strikes me as caused by a ridiculously high-speed fan combined with the zone bypass. A high speed blower/zone bypass combination is responsible for increased air speed stripping water from the cooling coil.
I grew up in a machine shop. So, when I was a student at the University of Minnesota, I lucked out and landed the APEX job of all time as a machinist in the Mechanical Engineering Research Machine Shop. Our mission was to build anything that the professors needed in their experiments and projects for their Doctorates. One of the professors I worked with experimented with solar panel heat collection. I built a solar panel out of a 4’ x 8’ sheet of copper and brazed a copper tubing line that snaked back and forth across the sheet. Then I added a smaller side panel that had no contact with the solar panel and could be set at any angle and direction as possible. We ran cold water into the tubing of the big panel and got amazingly hot water out the other end. Once that was working as best we could make it, he experimented by slanting the solar panel at different angles to work out a formula for effectiveness at various sun angles. As a sidelight he placed a drop of water on the small side panel at every angle and measured the temperature of the panel and the time it took the drop of water to run down hill one foot. The colder the panel and the closer to freezing, the slower the water would run. Therefore, the colder the coil the more adhesion to the coil. Not a huge difference but a definite measurable difference.
In this bypass situation, we definitely have a cold coil. But I am trying to put the pieces together. After this happens I want to understand the connection between cold coils, saturated with water and mold. I just cannot figure out what’s happening, but I have a lot of questions trying to sort it out.
Does the coil being overly saturated with
moisture increase the bypass factor? Is there a point where the bypass factor increases the face velocity through the coil and you get water blow-off?
The face velocity is a set number as explained below..
Coil Bypass Factor is the measured percentage of the air that travels through a coil that is not affected by the coil. It bypasses (doesn't touch) any cold surfaces of the fins, tubes, etc. This means that the discharge air from the coil is actually a mixture of air that is warm return air plus air conditioned air that is quite a bit colder. The bypass factor tells us the percentage of return air that makes its way through the coil without changing temperature. The Face Velocity of a coil is the cfm that the blower is putting out divided by the square foot area of the coil when looking at it strait on. Here are four examples of the bypass factor for a 3 tube coil with 14 fins per inch(I think this coil description is correct, I grabbed it out of some old work I was doing) (Dry Coil). Face Velocity (FV) 200 ft./min = (BPF) 0.07 which means that only 7/100 or (7%) of the return air is not cooled. (FV) 300 ft/min = (BPF) 0.11 or (11%) is not cooled. (FV) 400 ft/min = 0.14 or (14%) is not cooled. (FV) 0f 500 ft/min = (BPF) of 0.18 or (18%) is not cooled. Finally the fourth fundamental is: a rule resulting from experience and lab measurements. When the face velocity reaches over 500 ft/min, water is ejected from the coil and is not caught by the drain pan. A couple reasons for this is that the faster the air, the warmer the coil. The warmer the coil, the less adhesion it has for holding onto the condensate. So unnecessarily high speed air (Whether caused by a high speed fan or a zone bypass) is doing two things to your installation. It's decreasing the efficiency of the coil and sending condensate into the ductwork. Moisture and mold go together and the wet duct also adds to what is MISTAKENLY called re-evaporation from the coil.
In your white paper, you seem to imply that when you say "excess water takes up free space and reduces the amount of free area for air to flow at an efficient (500 ft. per minute) velocity through the coil. It has the same effect as reducing the size of the coil….."
My logic is: If a coil is loaded with water, that water takes up space. If this water is not blown out of the coil, the space for air to travel though is reduced and the air going through that space is moving faster. Thus a greater bypass factor combined with a lot of water flying off the coil and down the ducts, all the way to the mold’s Honeymoon Hotel.
I would assume that the saturated coil would re-evaporate humidity when the discharge air sensor shuts the compressor off….
That’s logical.
What do the psychometrics look like under these conditions? Are those conditions conducive to mold?
I don’t have a clue about the psychometrics that might be conducive to mold growth! What I know is if you have water in dark, dank ductwork, you’ve got a big problem and better take care of it!
What happens when and if the evaporator coil freezes, then thaws out when all zones are calling?
It sprays a LOT of water into the ducts!
I would really appreciate and value your thoughts and scholarship on this topic.
Danny Gough
Energy Solutions, Inc.
Thanks for the opportunity!
Richard Peters,
P.E./CM The HVAC/IAQ Whisperer
This email address is being protected from spambots. You need JavaScript enabled to view it.